How Do Compression Springs Work?
Compression springs store and release energy when subjected to a compressive force. As the spring compresses, it stores energy within its structure. When the force is removed, energy is released and the spring expands to its original length. They are used in various products and applications, from smaller household items to larger industrial machinery, including pens, garage doors and vehicle suspension systems.
Once we understand how compression spring mechanisms work, we can use them in various applications such as shock absorption, vibration dampening, and maintaining contact pressure. This post will explore:
The Basics of Compression Spring Mechanism
Compression springs provide a versatile and efficient way of absorbing compression. The typical design for a compression spring is a helical wire coil spring, giving them their alternative name, compression coil springs. These springs come in various shapes and sizes, including conical compression springs and cylindrical ones, to suit their applications' specific needs.
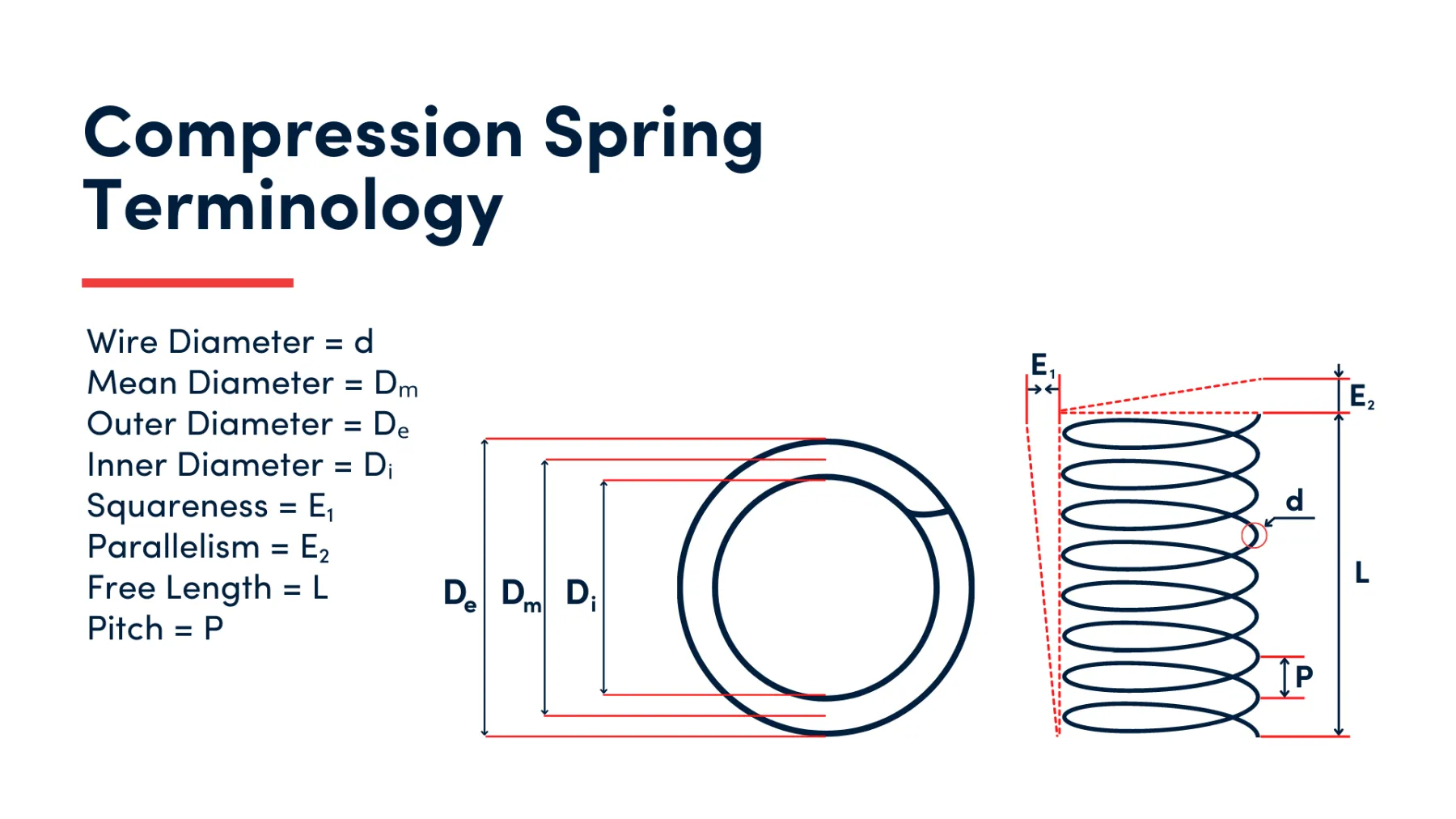
Elastic Deformation and Hooke's Law
When a compression spring is subjected to a compressive force, its length reduces. This process is called deformation (also known as deflection). However, when the force is removed, it will return to its original length; the ability to return to its original shape is a fundamental part of a compression spring's functionality.
Hooke’s Law describes this process, which states that the force is directly proportional to the displacement. This can be written as the equation: F = k * x, where F is the force, k is the spring constant (stiffness), and x is the deflection.
Stress and Strain in Compression Springs
Stress is the force that tries to compress a spring; it is typically measured in Pascals (Pa) or Megapascals (MPa), or pounds per square inch (psi) in the imperial system.
Strain is the change in length relative to the original length of the material. Strain can be calculated using a simple formula > Strain = change in length/original length of the material.
Spring Constant and Its Significance
The spring constant is a measure of the stiffness or rigidity of a spring. A higher spring constant makes a stiffer spring; this means it requires a higher compression force to shorten the length of the spring (deflection). The ‘spring constant’ concept allows engineers to create specific springs to meet certain performance requirements. It is essential for understanding, designing and predicting the behaviour of springs in various applications.
Compression Spring Design
Several factors must be considered when designing compression springs. Factors include the load requirements, the deflection (deformation) requirements, the material, the number of coils, the spring parameters and stress and deflection limits. Considering the above, engineers can design compression springs that meet specific application requirements and balance these factors with manufacturing costs and feasibility.
Key Design Parameters
Many factors may affect the design of a compression spring, and by considering these, an engineer can produce springs that meet specific requirements while being aware of costs, overall performance, and durability.
Material Selection for Compression Springs
The material properties of a compression spring directly impact its performance as they determine its strength, durability, and resistance to deformation.
Compression springs can be made from a wide range of materials, including Carbon Steel, Stainless Steel, Chrome Silicon, Chrome Vanadium, Phosphor Bronze, Beryllium Copper, Inconel Alloy, Titanium Alloy, Nitinol (Nickel Titanium) and Plastic (Acetal, Nylon). Material selection is crucial to ensure a spring can provide the required support under compression without exceeding its elastic limit. Other factors to consider when selecting a material include temperature range and corrosion resistance. Engineers conduct material testing to ensure the chosen material meets the requirements of the application.
Compression Spring Calculator
The equation used is: F = k * x, where F is the force, k is the spring constant (stiffness), and x is the deflection of the spring. We can then use two useful formulas to calculate Spring Rate and Load Capacity.
The Spring Rate is the load variation per deflection unit (deformation). We can calculate this using the formula below:
Spring Rate Calculation:
Spring Rate = Force Applied / Deflection of the Spring
*spring rate is measured in newtons per meter (N/m) or pounds of force per inch (lb/in)
*force applied is measured in Newtons (N) or pounds (lb)
*deflection is measured in mm or in
The Load Capacity is the maximum amount of Newtons a spring can withstand before it is at risk of buckling or permanent deformation.
Load Capacity Calculation:
Load Capacity = Spring Rate x Maximum Allowable Compression
*load capacity is measured in Newtons (N)
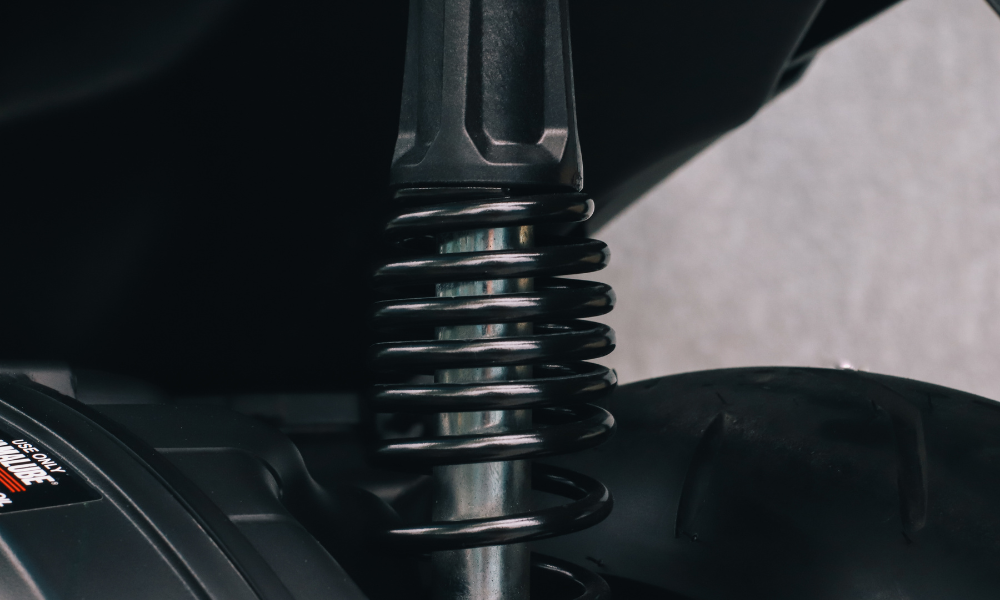
Forces and Deflection in Compression Springs
When a compression spring is subjected to a load, it experiences forces that cause it to deflect (deform) or change shape. Understanding the relationship between these forces and the spring’s deflection is crucial for designing springs that can efficiently store and release energy while maintaining structural integrity. By understanding these forces and deflections, engineers can design resilient springs that are more appropriate for their intended applications.
Exploring the Force-Displacement Relationship
Hooke’s Law states that the displacement of a compression spring is directly proportional to the applied force, meaning that as the applied force increases, the spring's displacement also increases. This relationship is essential for understanding how compression springs store and release energy.
Load (force)
The force the spring is required to support.
Free length
The length of a spring when no force is applied.
Spring constant
The stiffness or rigidity of a spring.
Wire diameter
A spring wire's diameter (affects strength and flexibility).
Coil diameter
A coil's diameter (influences the space requirements).
Spring Index
This is the ratio of mean coil diameter to wire diameter, which affects stress distribution.
Number of coils
The total number of coils in the spring (affects flexibility and response to load).
Deflection (deformation)
The amount of deformation a spring will experience when the force is applied.
Elastic limit
This refers to the maximum amount of force that a spring can undergo while still being able to return to its original shape.
Solid height
The length of a spring when fully compressed.
Material type
The type of material used to make the spring.
Buckling considerations
A spring may buckle under certain compression levels.
End Conditions
The design of the ends of a spring, e.g. open, closed and squared, closed and ground or double closed ends.
Permanent deformation
The consideration that springs may experience permanent deformation over time.
Equilibrium Position and Solid Height
The equilibrium position of a compression spring is the point at which the spring is at its natural length, neither stretched nor compressed. This point is the benchmark for measuring displacements (deformation) and supports an engineer in assessing how a spring reacts when exposed to compression or force. The solid height of a compression spring is when it is fully compressed; in this state, all of its coils touch one another. Understanding the concepts of equilibrium position and solid height is crucial for designing compression springs that can efficiently store and release energy while maintaining structural integrity.
Spring Rate and Load vs. Deflection
The Spring Rate is the load variation per deflection unit (deformation). A higher spring rate indicates a stiffer spring that can handle a more significant load and will experience less deflection. A lower spring rate means a softer spring with a lower load capacity, which, in turn, will experience more deflection.
Manufacturing Compression Springs
The manufacturing process of compression springs involves a series of steps, including coiling, heat treatment, and surface finishing. Each process ensures the spring’s highest performance, strength, and durability. In this section, we will discuss the various manufacturing processes involved in producing compression springs and the different surface finishes and coatings available to enhance their performance and longevity.
Coiling Process and Variations
The coiling process is a crucial step in the manufacturing of compression springs. This process uses specialised coiling machines, which ensure precise control over the pitch, coil diameter, and number of active coils. During the coiling process, various variations can arise, such as variations in pitch (distance between coils) and diameter. The coiling process, along with subsequent heat treatment and finishing steps, determines the final characteristics and performance of the compression spring.
Heat Treatment for Stress Relief
Heat treatment is a critical step in the manufacturing process of compression springs, as it helps to reduce residual tensile stresses and remove induced stresses caused by the coiling process. This results in improved performance and durability for the spring. There are several methods for heat treatment, including annealing, stress relieving, and spring setting treatment. Appropriate heat treatment is vital to ensuring the performance and longevity of compression springs.
Surface Finish and Coating Options
The surface finish of a compression spring is an essential factor that directly impacts its performance and longevity. The correct surface finish can reduce friction, extend the spring’s fatigue life, and improve its corrosion resistance. Each surface finish and coating option has pros and cons - it is essential to consider the specific requirements of the compression spring application before selecting a finish or coating.
Compressions Spring Examples
Compression springs are incredibly versatile and have uses in various industries. They are used in automotive suspension systems, industrial machinery, aerospace and aviation, medical devices, consumer electronics, furniture and bedding, toys and games and sports equipment. Their ability to store and release energy efficiently makes them an essential component in many applications.
Automotive Suspension Systems
Compression springs play a key role in automotive suspension systems. They absorb shock and resist compressive forces, ensuring the vehicle’s stability and ease of handling. Compression springs work with other components, such as dampers, to optimise the overall performance and handling of the suspension system.

Industrial Machinery
Compression springs are used in various industrial machinery, providing resistance and absorbing forces to ensure components' smooth operation and movement. They are used in manufacturing, transportation, construction, agriculture, petrochemical, and other industrial sectors. Some examples of industrial machinery that utilise compression springs include construction equipment, agricultural machinery, medical devices and precision instruments.
Factors Impacting Compression Spring Behaviour
The performance of compression springs is affected by various factors, including their mechanical properties, design parameters, and the conditions under which they operate. Engineers may use mathematical models, simulations, and testing to optimise spring designs for specific conditions and load requirements.
Temperature Effects
The temperature at which a compression spring operates can significantly impact its performance; the spring material may either expand or contract when exposed to different temperature environments. It is also possible for the material properties to change due to heat or cold exposure.
Fatigue and Spring Life
Fatigue and spring life are critical considerations when designing compression springs, especially when the springs undergo cyclic loading or repeated compression and relaxation. Fatigue refers to cumulative damage that occurs when a material is subjected to repeated loading and unloading cycles, leading to the eventual failure of the material. Understanding fatigue is crucial for predicting compression springs' life expectancy and reliability.
Interestingly, a study titled
‘Stress relief effect on fatigue and relaxation on compression springs’ found that when they reduced heat treatment time (in a 400 °C group), the fatigue limit did not change. This result will differ depending on the materials used; however, it shows that a cost reduction may be viable in this manufacturing process. This shows how engineers can weigh up the pros and cons of certain materials, the intended use of application and the cost involved in production.
Stress Relaxation
When subjected to a constant load over time, stress relaxation happens to materials, including those used in compression springs. It involves a gradual decrease in stress within the material, even though the load remains constant. This is important to consider in applications where compression springs are used for extended periods, as it can affect the spring's overall performance. Choosing materials with low relaxation rates significantly reduces the risk of stress relaxation in springs.
Summary
Compression springs are a highly versatile and efficient way of absorbing force in various industry applications. The manufacturing process involves various materials with multiple properties, and engineers must choose materials appropriate to the spring application. Equilibrium position, solid height and spring rate affect a spring's performance, as does the manufacturing process, including coiling, heat treatment and surface finish.
Many factors affect compression spring behaviour, and these need to be carefully considered, as do precautions in installing, handling and maintaining springs.
If you would like to find out more about the different types of compression springs, you can check out our compression spring information page. We also have a glossary of spring terminology, which can help you better understand various elements and other types of springs.
LESJÖFORS
Get in touch. Please leave an enquiry by filling in the form or contact us by phone or email, reaching our offices using the options below.
Get in touch with a Specialist